The rudder of a Saare Yacht
The rudder is an important and safety-critical component on any sailing yacht.
A well-designed profile, an appropriate aspect ratio, a narrow gap between the hull and the rudder, and maximum strength are essential. The rudder blade has a significant influence on the sailing characteristics and steering behavior. The degree of forward balance is particularly important for achieving optimal and energy-efficient autopilot steering. The rudder’s positioning also plays a crucial role in maneuverability.
Two rudder blades offer advantages when sailing with very wide stern hulls at high heel angles. However, the mechanism for connecting the two rudders and steering is complex and somewhat less responsive.
There is a drawback when maneuvering in tight spaces in a harbor: targeted reverse motion is not possible without bow and stern thrusters. The propeller stream does not hit a centrally positioned rudder blade but flows between the two blades.
A single rudder blade, centrally positioned under the hull, enables precise and straightforward reverse maneuvers in a harbor. The boat can turn tightly, and the propeller’s flow is optimally directed.
We install rudder blades that extend deeply enough into the water. However, our rudder blades are always less deep than the keel to avoid damage in the event of grounding.
With the combination of a deep-reaching rudder blade and the relatively narrow hull of a Saare yacht, it is almost impossible for the feared flow separation at the rudder blade—and the subsequent “round-ups” (loss of control)—to occur.
The Rudder of a Sailing Yacht is Subject to Significant Loads and Forces
Construction of Rudder Blades
We manufacture the rudder blades for the 38- and 41-foot models in-house.
To do this, we laminate several layers of fiberglass laminate with vinyl ester resin into two molds. On one side, the rudder shaft is inserted and laminated into place with several layers of fiberglass.
The rudder shaft on our yachts is always made of stainless steel. Although significantly heavier, it is much more corrosion-resistant. The aluminum rudder shafts commonly used are very vulnerable, especially when copper-based antifouling paints are applied.
These two halves of the rudder are bonded together, and the molds are securely bolted. A precisely calculated amount of liquid epoxy foam is poured into the cavity, which quickly expands and fills the entire volume with high-strength, waterproof epoxy foam.
A rudder blade built this way is robust and durable. Vinyl ester as a laminating resin and the epoxy foam filling make the rudder resistant to osmosis. The stainless-steel shaft prevents pitting corrosion, which is common with aluminum shafts.
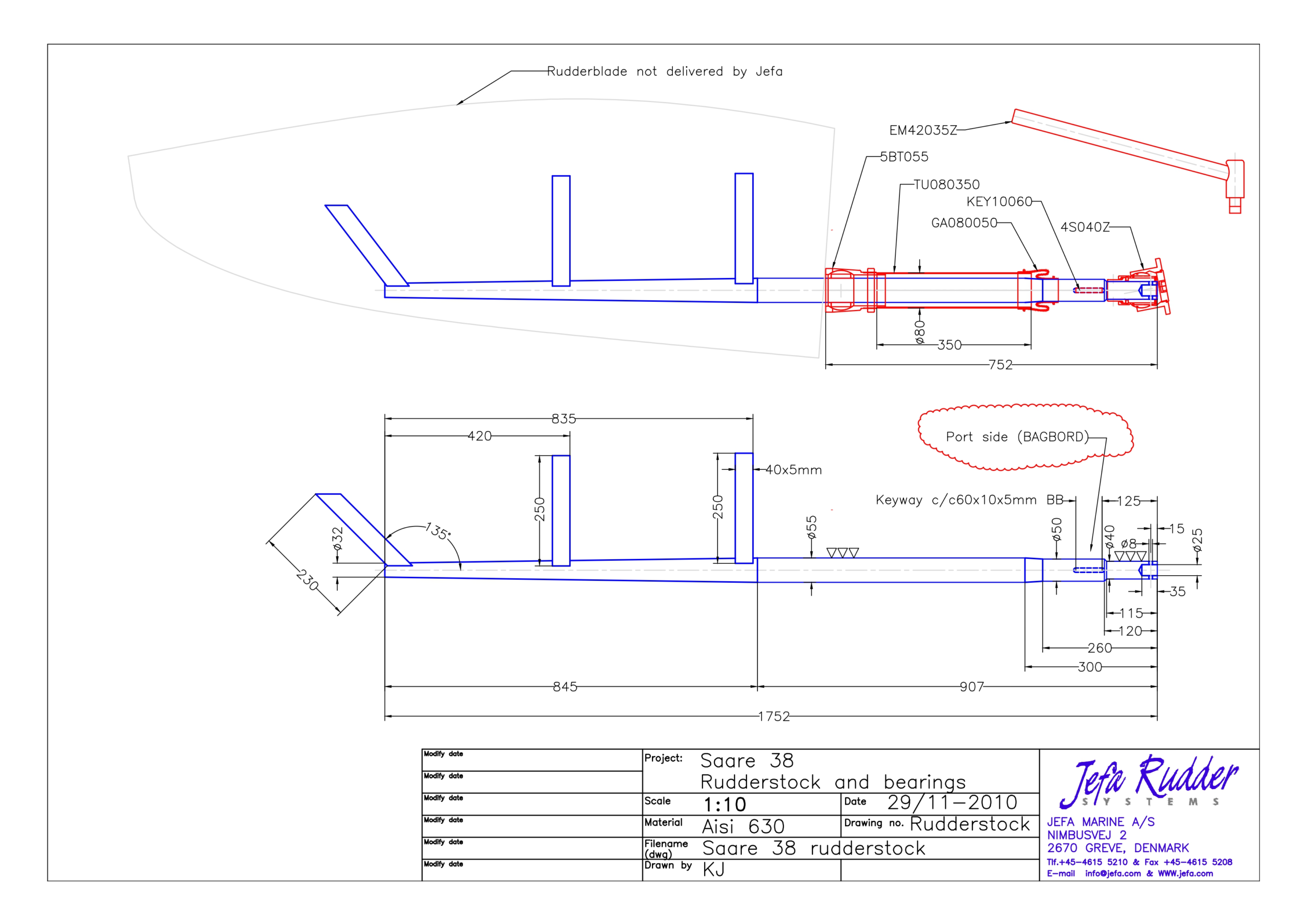
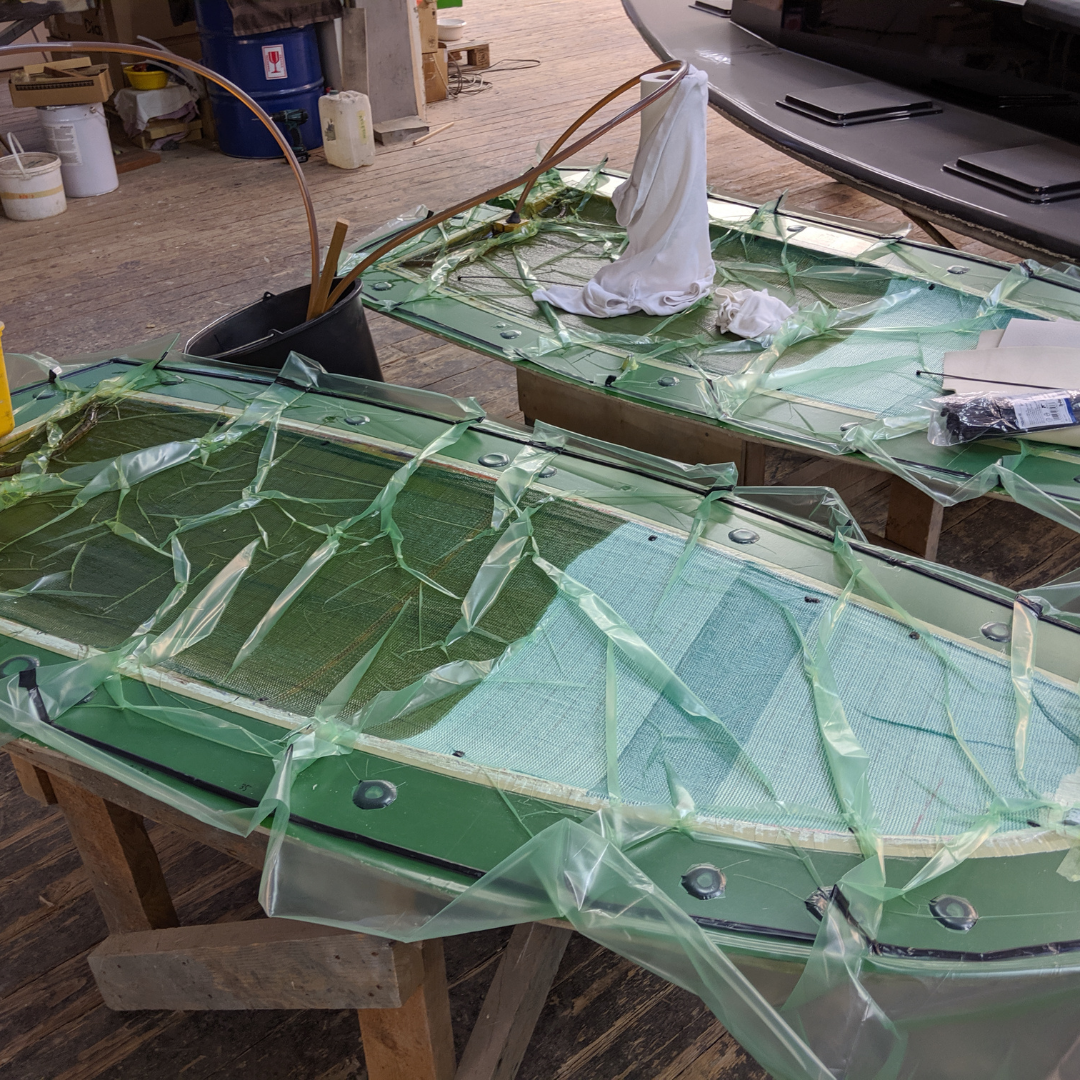
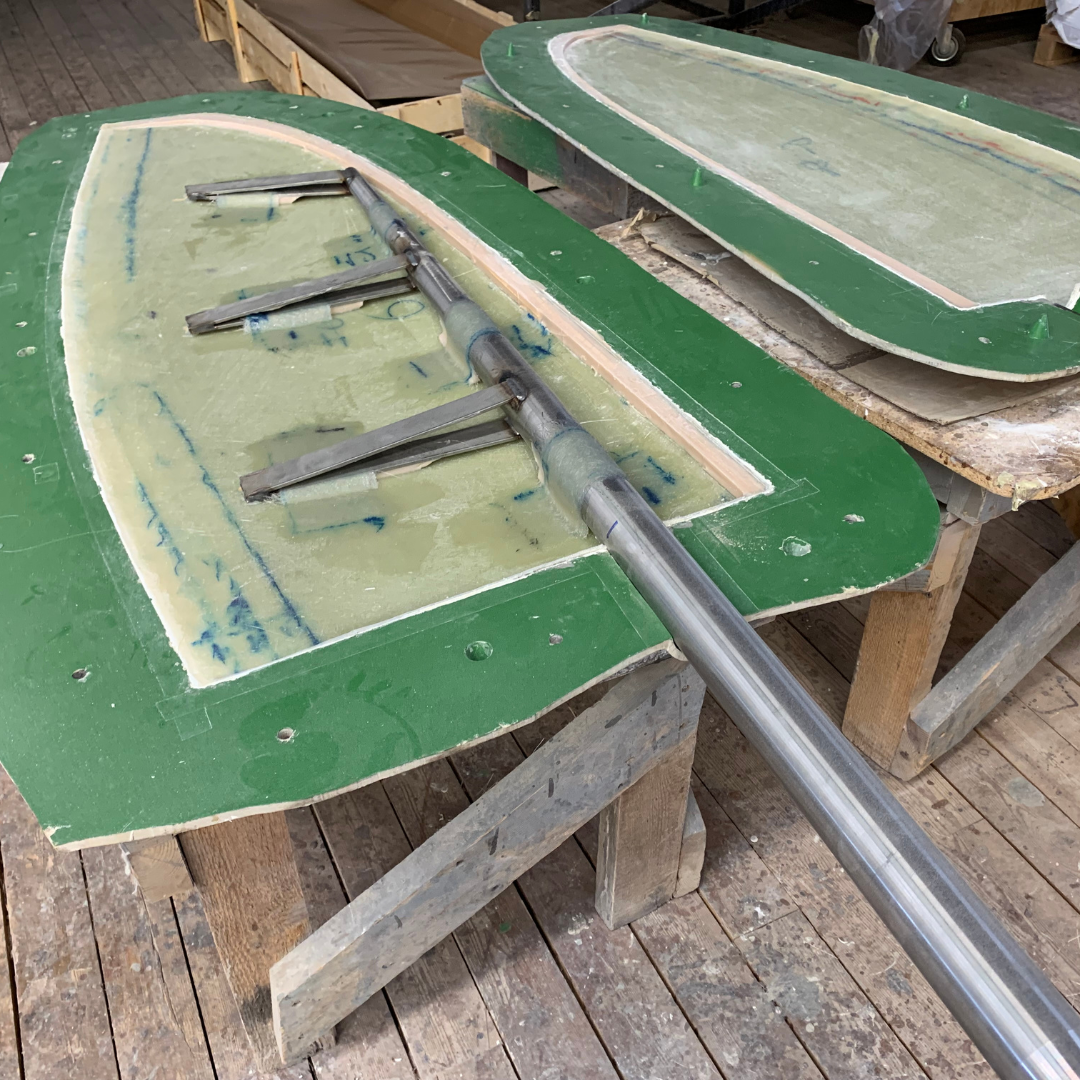
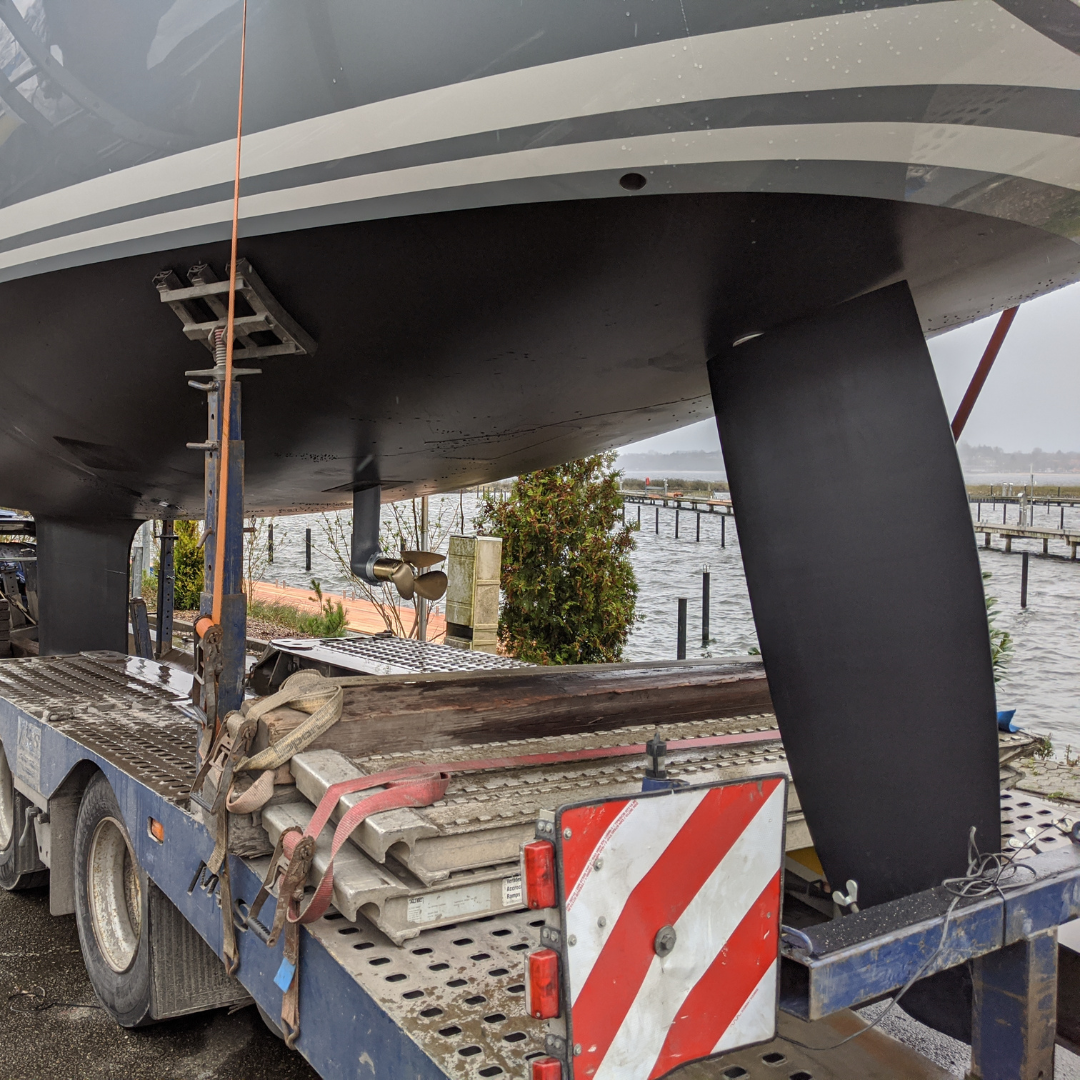