All Saare yachts are built using the contemporary vacuum infusion process.
In 2015 we started building the hulls of the Saare yachts using the modern vacuum infusion process. This construction process has been technically mature and proven for many years and many renowned shipyards use it.
There are clear advantages:
- The component becomes significantly lighter and yet stronger and more stable.
- The proportion of glass in the laminate increases and therefore the strength and density improves.
- Air pockets are avoided by the vacuum and the risk of osmosis is practically eliminated.
- Environmental problems and health risks for workers are significantly minimized.
- The entire fiberglass work is cleaner, more controllable and always exactly the same.
- The hull and deck become lighter, around 500 kg for the Saare 41ac.
- This improves the ratio of total weight to keel weight and the boat sails stiffer and safer.
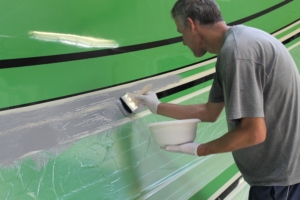
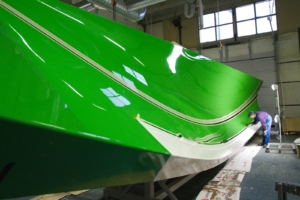
The gelcoat must also be applied by hand in the area of the rubbing strip. If you were to spray gelcoat there, the layer in the narrow, narrow profile would quickly become much too thick. Then there would be a risk that the gelcoat would later easily crack and flake off.
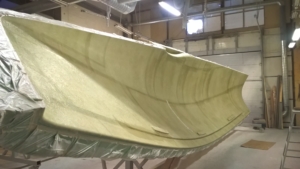
The first two fiberglass layers are carefully laminated with special surface mats using the hand-laying process. They stabilize the gelcoat and prevent the stronger fibers of the rovings and mats from pushing through later in the vacuum process and showing in the outer skin.
At Saare Yachts, all laminate layers are always laminated with high-quality and extremely water-resistant vinyl ester resin.
The protection against osmosis is therefore perfect. The molded parts for the hull windows and the beading of the rubbing strip are clearly visible here.
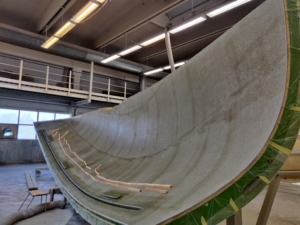
The profile of the rubbing strip must be particularly stable. After several layers of laminate are placed there by hand, it is massively filled.
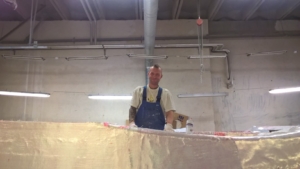
Finally, this area is smoothed with a filler and then the various glass scrims are added, which are placed dry into the mold.
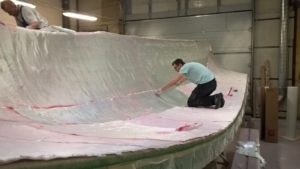
Risto and Jüüri then place the fiberglass mats and glass scrims into the mold. A second team with Janek and Mariza is working on the other half of the fuselage. The glass layers are fixed with a spray adhesive (red).
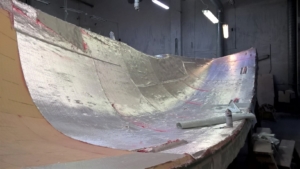
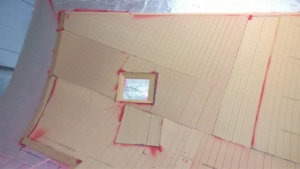
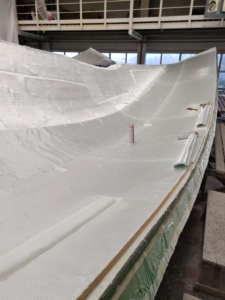
The foam is carefully laid, fixed and triangular profiles are connected to the edges to create “soft transitions”.
The foam is left out at all hull openings.
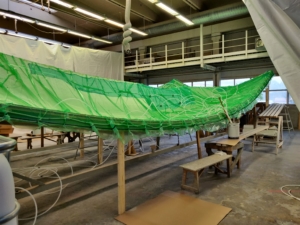
The inner glass layers are then laid out from the foam. All glass layers, as well as the foam, are fixed with a spray adhesive (red).
We work a lot with combination mats, which are glass layers made of interwoven fabric/roving and glass mat.
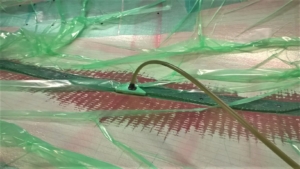
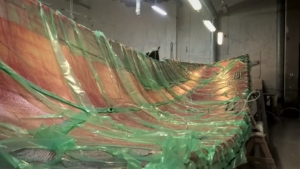
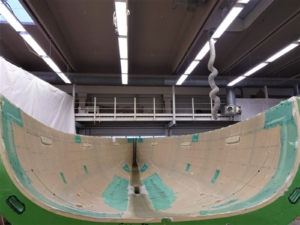
The photo above shows the beginning of the infusion process. It is easy to see how the resin, starting from the feed point, runs through the entire material structure and saturates the foam and the glass.
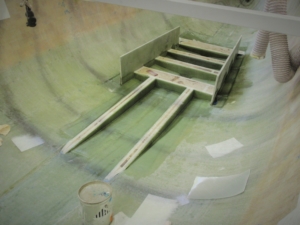
In the photo below you can clearly see that after a little more than an hour the resin has permeated the entire structure, all fiberglass and sandwich foams are soaked with resin and the infusion is complete. There is no more air in the vacuum package; the vacuum compresses the laminate structure.
The vacuum then remains for around 20 hours until the structure has hardened. The foil can then be removed and the vacuum infusion process is completed.
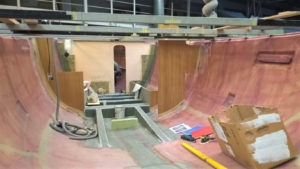
Both fuselage halves are fitted together precisely and then connected to each other very carefully and securely. To do this, many layers of solid laminate are laminated in the middle of the boat; this important part of the yacht must be very strong and solid. The material thickness in this area is up to 40 mm.
The hoses from the infusion process are still in the fuselage, and you can clearly see the cutouts for the fuselage windows and the recesses in the sandwich in the places where fuselage breakthroughs will later be installed.
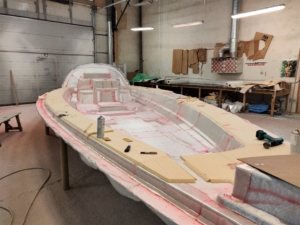
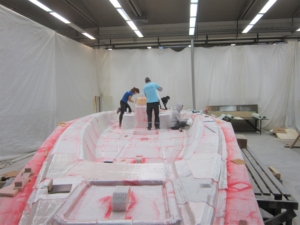
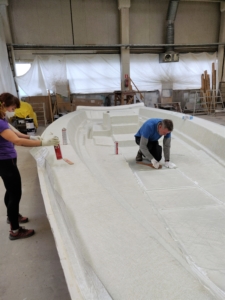
Finally, the film is placed over the component in an airtight manner and the resin is sucked in. Air and excess resin are sucked out, the component is perfectly and evenly saturated with resin. The laminate is perfectly ventilated, has a high density and is more stable than a hand laminate.