Why is the keel on a Saare yacht better than on almost all other sailing yachts?
Will Saare Yachts soon be the last shipyard to build with such great effort?
While other shipyards are increasingly moving away from the best keel construction, with a deeply laminated bilge and a lead keel bolted into the bilge under the yacht, for cost reasons, we are sticking to this solution.
There is nothing better!
In addition to the optimized sailing characteristics, this construction method ensures maximum safety in the event of a grounding.
Even a strong grounding will not cause serious damage to the hull, the repair is usually only cosmetic and inexpensive.
(Of course, we cannot always rule out damage to the hull in the event of a very serious grounding.)
When comparing with other shipyards, make sure that all yachts, and not just the older models, really meet these high standards.
A keel that is screwed under the flat bottom of the boat transfers the forces that occur when sailing, and especially the forces of a heavy grounding, much more strongly and directly to the hull. The damage to the hull and the boat can be quite significant if the boat touches the ground.
The entire keel of a Saare yacht is made of lead. (antimony hardened lead)
Lead keels are rarely used today; they are significantly more expensive compared to a cast iron keel.
In addition to a maximum low center of gravity and thus optimized sailing properties, lead naturally has the great advantage of not rusting. This makes a lead keel much easier to care for and the whole boat better.
The specific gravity of lead is around 1.6 times higher than that of cast iron. This means that the keel profile can be designed to be slimmer and the center of gravity is lower.
Now you might think that rust on the keel, e.g. after a light contact with the ground and scraping off the paint build-up, is no big deal. That’s true, it doesn’t cause any technical problems and it’s just a visually ugly thing.
However, the rust corrosion is critical at the seam between the cast iron keel and the hull. Sooner or later, every cast keel begins to rust at this connection to the hull, no matter how the keel is attached. This rust spot is then practically impossible to remove permanently.
You can only have peace of mind for a few years if you remove the keel completely, clean the hull and the keel surface very thoroughly and then sand the keel clean and re-prime and coat it several times on the contact surface and a few centimeters on the sides. It is best to remove the rust in this area using sandblasting; sanding does not completely remove the rust from the pores. Then, after a multi-layer paint build-up, you can reassemble the keel with adhesive and sealant and re-seal the surrounding seam with a permanently elastic material (e.g. Sikaflex, Tikal, Pantera, etc.).
If you don’t do anything about this increasingly rusting seam, over the years the rust surface will move deeper and deeper into the joint and onto the surface of the keel. It undermines the bond between the keel and the hull and removes it. Water penetrates deeper and deeper and the sealing of the keel bolts can become leaky.
The entire keel is no longer firmly and securely attached to the boat.
With a lead keel these risks are eliminated! Lead doesn’t rust.
An at least equally important argument in favor of a lead keel is the elastic deformability of the material.
If a cast iron keel hits the ground strongly, it will only get a few scratches at the point of contact with a stone or rock, but due to the material properties (high modulus of elasticity), it transmits the impact very directly and undamped to the hull. Strong tensile forces then occur, particularly at the front edge of the keel; at the aft edge of the keel, the narrow and pointed keel is pressed hard and powerfully into the hull.
Depending on the construction and quality and the design of the keel fastening, this can lead to serious and severe damage to the hull and also to the internals in the boat, depending on the impact and the speed of the boat.
Although it is usually possible to repair such groundings, the costs can quickly amount to tens of thousands of euros or much more.
Particularly if the reinforcements in the bilge (bottom wrangles and stringers) consist of a steel structure, this can partially or completely come off and often has to be completely removed for repairs. The effort can then be so great that a repair is not economically worthwhile.
Even with a lead keel, damage to these areas cannot be ruled out. However, they only occur at significantly higher speeds and even then only to a reduced extent. The reason is the high plasticity and good formability of the relatively soft material lead. The modulus of elasticity of lead is 5 to 7 times lower than that of cast iron, i.e. lead is significantly softer and more plastic. The lead deforms significantly at the point of impact and thus takes away a lot of energy from the impact. The forces between the keel and the hull and therefore the damage to the hull and the interior are correspondingly lower. The dented and compressed lead can easily be filled with epoxy filler and painted with antifouling.
The material of the keel and the type of installation are also of utmost importance for the sailing properties. A keel should not be too heavy and increase the total weight of the yacht, but it should ensure that the center of gravity of a sailing yacht is as low as possible. Of course, this is easier to do with lead than with a cast iron keel. In addition, the keel on a Saare is attached to a deep, strong laminated bilge and is therefore around 40 to 50 cm lower than the usual construction.
If you compare different yachts and calculate the ratio of keel weight to total weight, the so-called ballast proportion, this statement is not very meaningful without including the center of gravity of the keel in the considerations for the righting moment. Saar yachts have relatively heavy keels (37 to 41% ballast content) and these keels are mounted well below the bottom of the hull on the deep S-frame bilge.
The righting moment of the Saare keel construction is particularly high.
The performance when sailing is better with a lead keel.
The shipyard Saare Yachts OÜ buys the keels from a foundry in Finland. The quality is very good, the surfaces are smooth and strong. 14 keel bolts made of stainless steel, each with a 24 mm diameter and metric thread, are cast into the solid lead keel of the Saare 41 with a connecting frame, also made of V4A steel. The distance between the adjacent bolts is large and the force application is perfect.
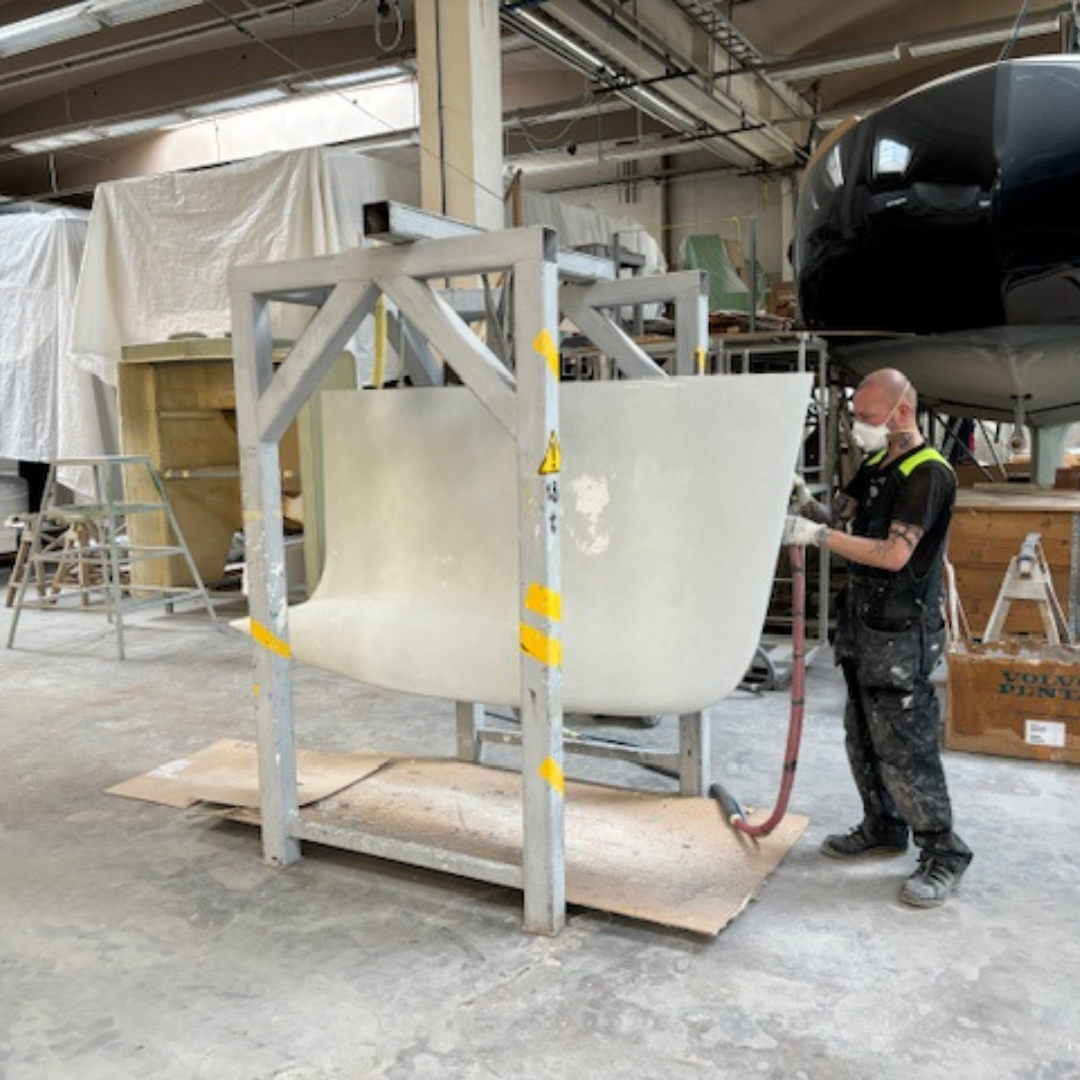
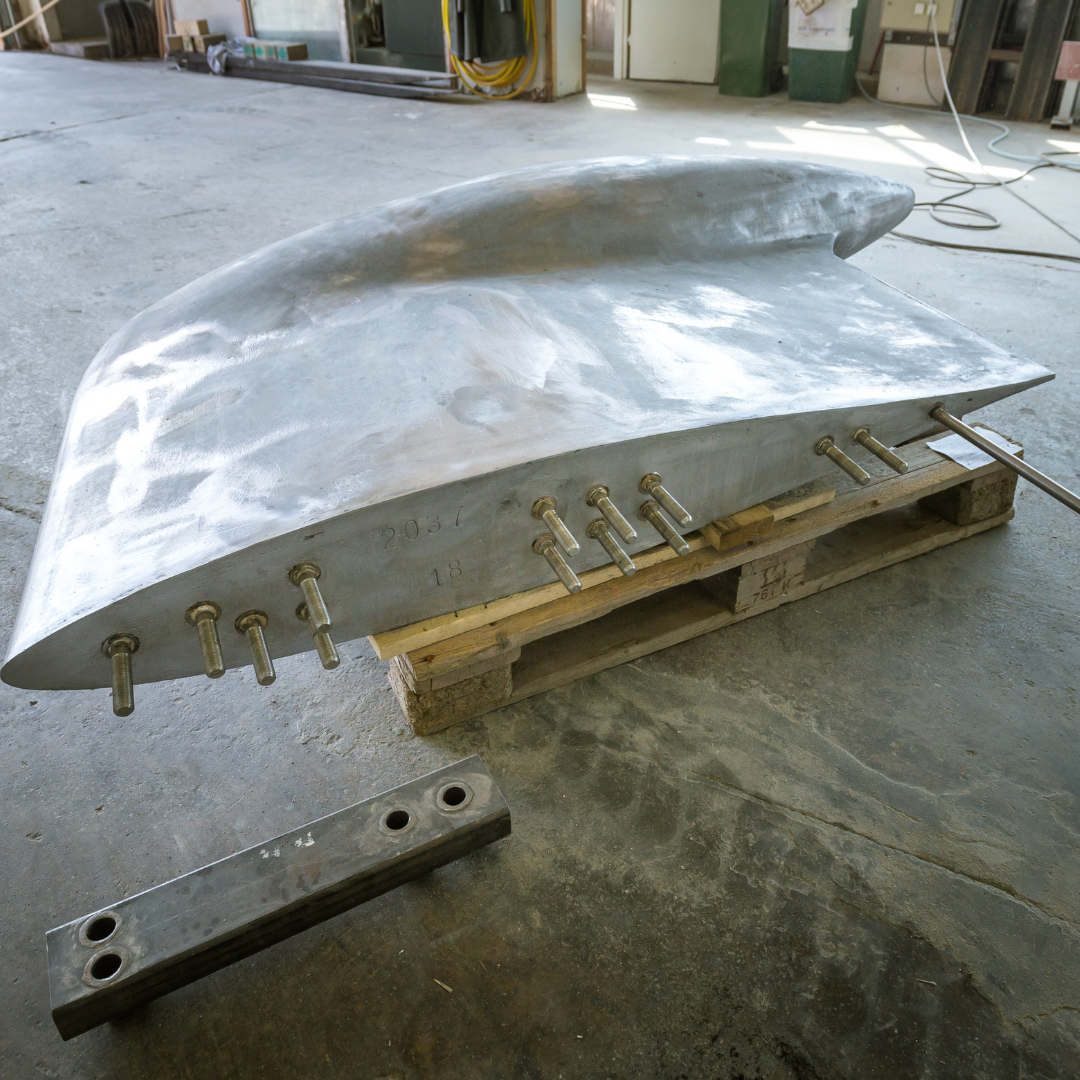
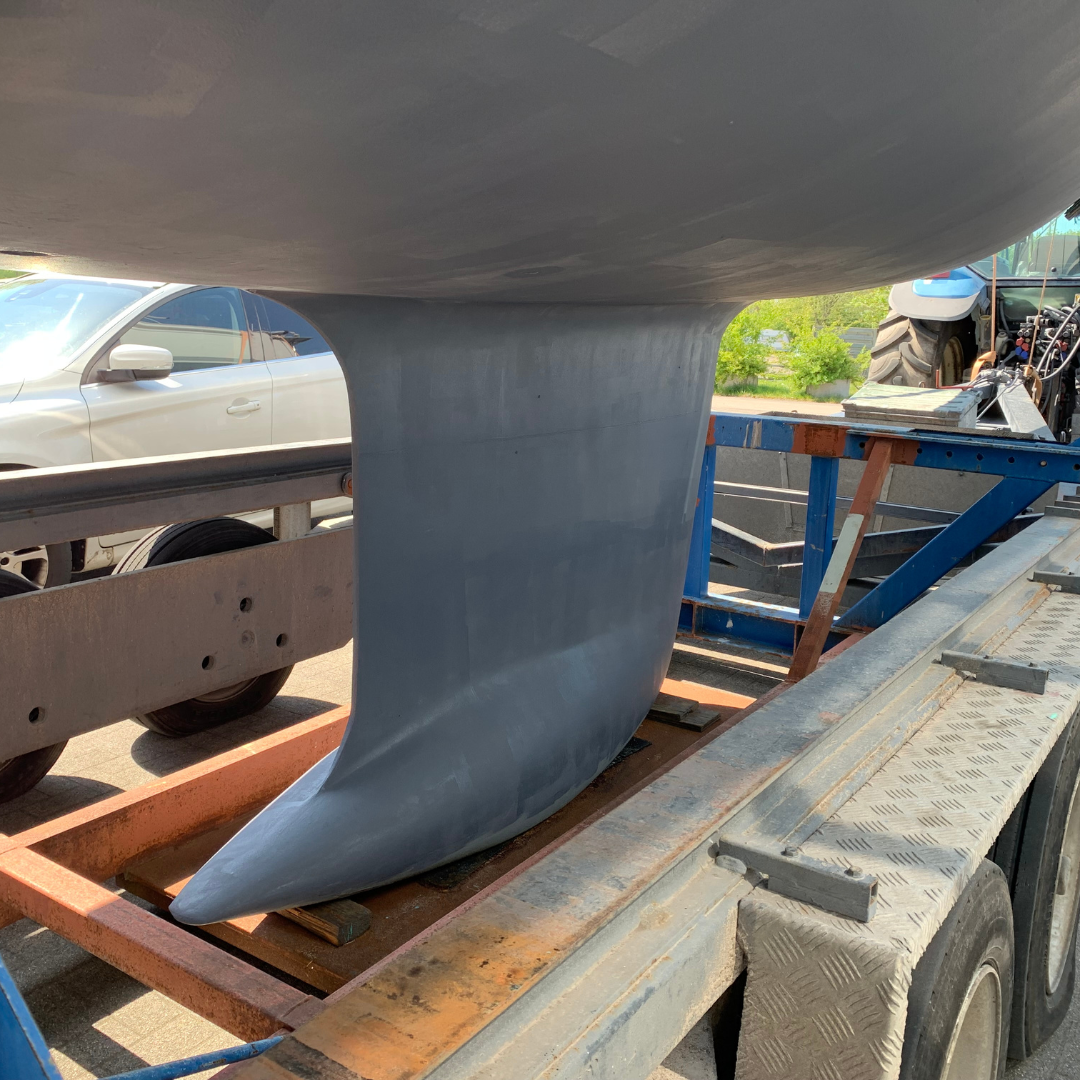
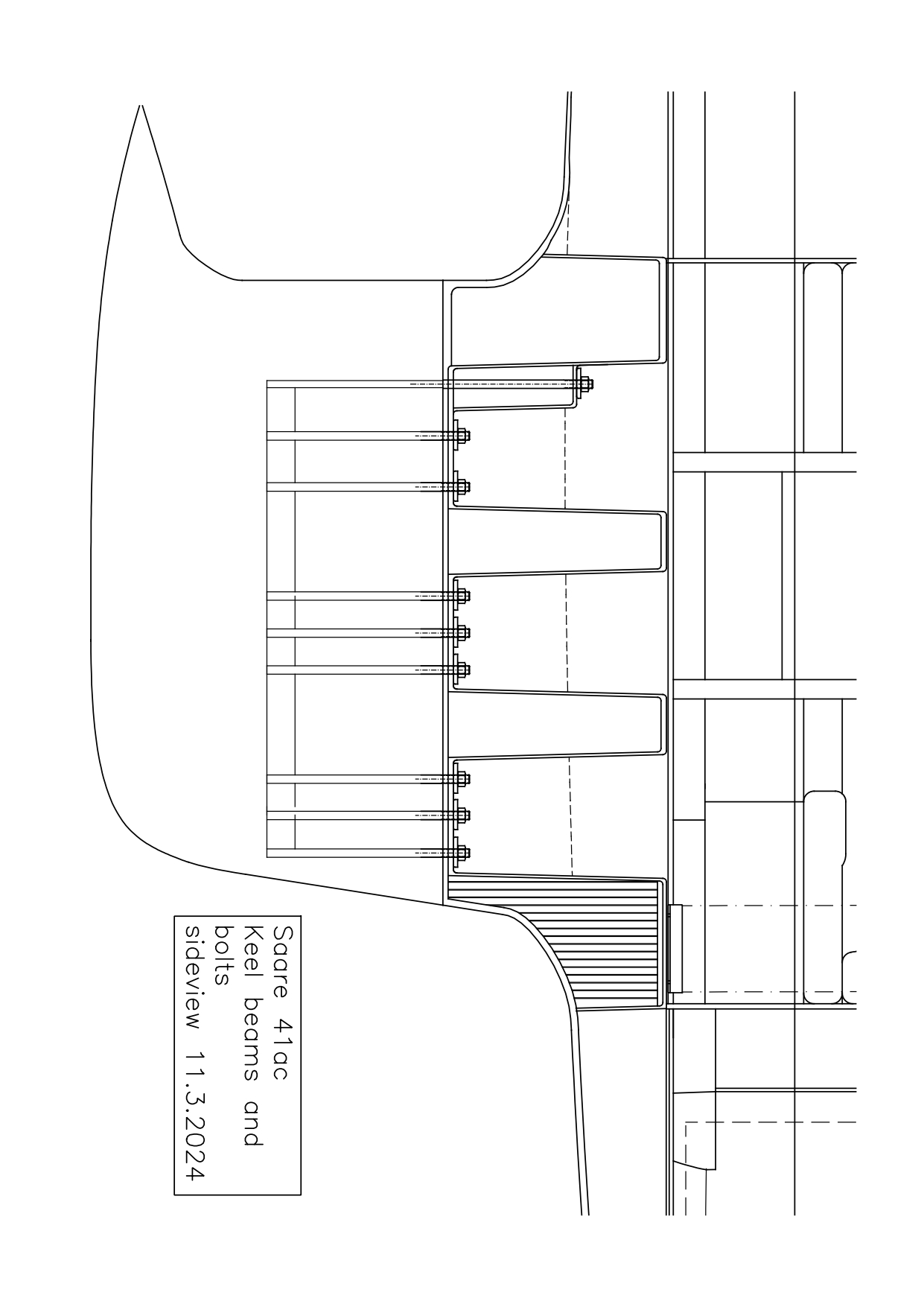
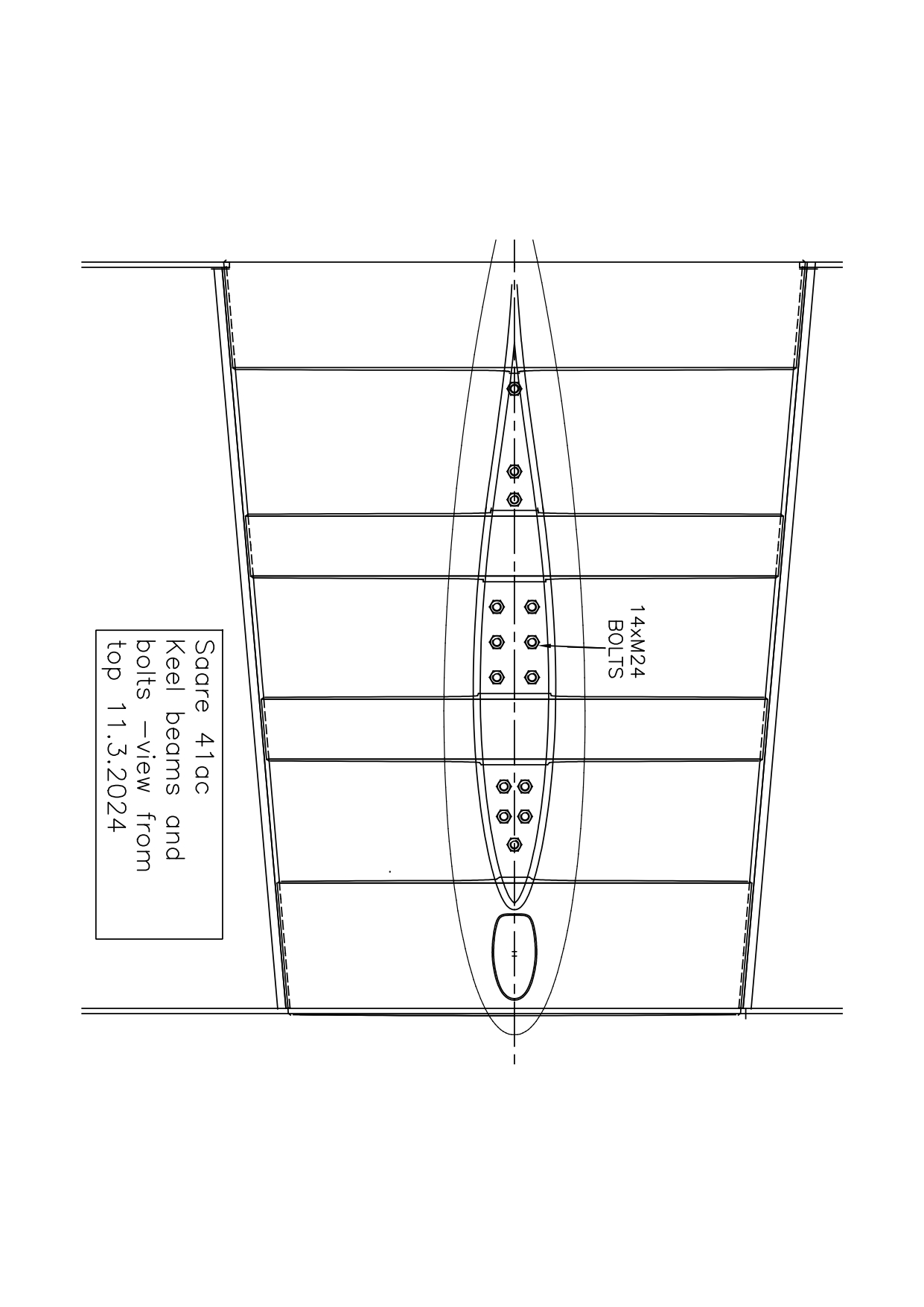
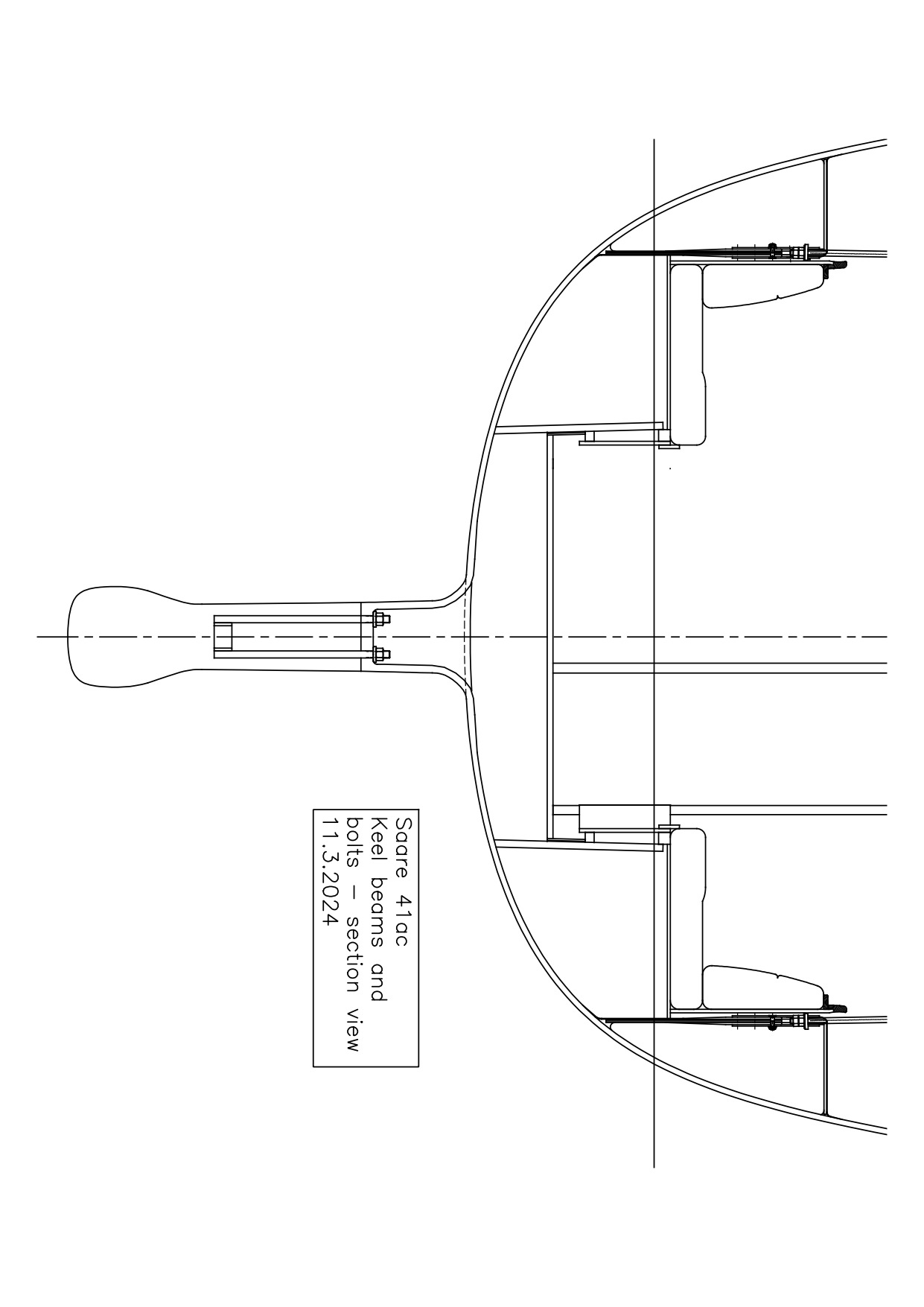